2022年7月8日(金)、「CGWORLD デザインビズカンファレンス 2022 夏」が開催された。本イベントは、建築、製造、アパレルなど、各業界の最新のデザインビズが学べるカンファレンスイベントで、多数の企業や技術者たちが登壇。今回はその中で、株式会社GKダイナミックスによる「Fusion360を使用したヘルメット開発」の講演内容をお届けする。
関連記事
・3Dプリントによる"ワークフローの最適化"とは? 日南に聞くプロダクトデザイナーへの道のりと、業界の未来~CGWORLD デザインビズカンファレンス 2022夏(1)
・3Dサンプルが創出する新たな可能性。デジタルクロージングが"バーチャル試着"で目指すもの〜CGWORLD デザインビズカンファレンス 2022夏(2)
イベント概要
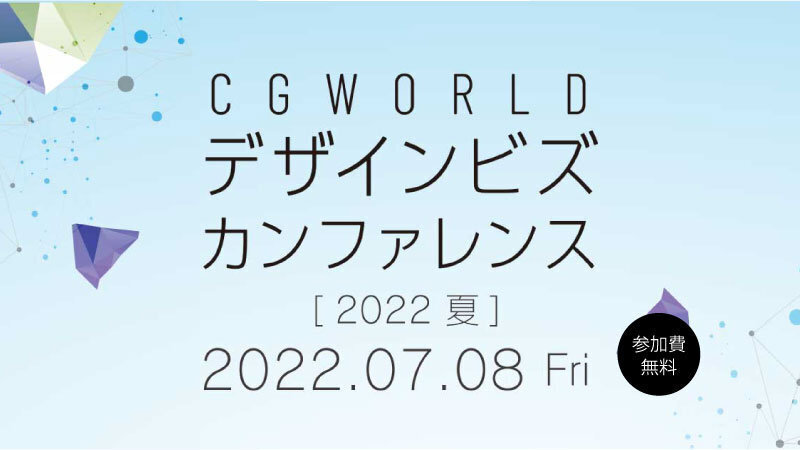
CGWORLDデザインビズカンファレンス2022夏
開催日:2022年7月8日(金)
時間:13:00~18:30
場所:オンライン配信
参加費:無料 ※事前登録制
cgworld.jp/special/cgwviz2022/summer/
先代モデルを超えるシンプルで機能的なデザインを追求
今回登壇したのは、GKダイナミックスでデザインディレクターを務める本田宗久氏。本田氏は2000年に同社に入社後、パーソナルモビリティデザインに多数携わっている。
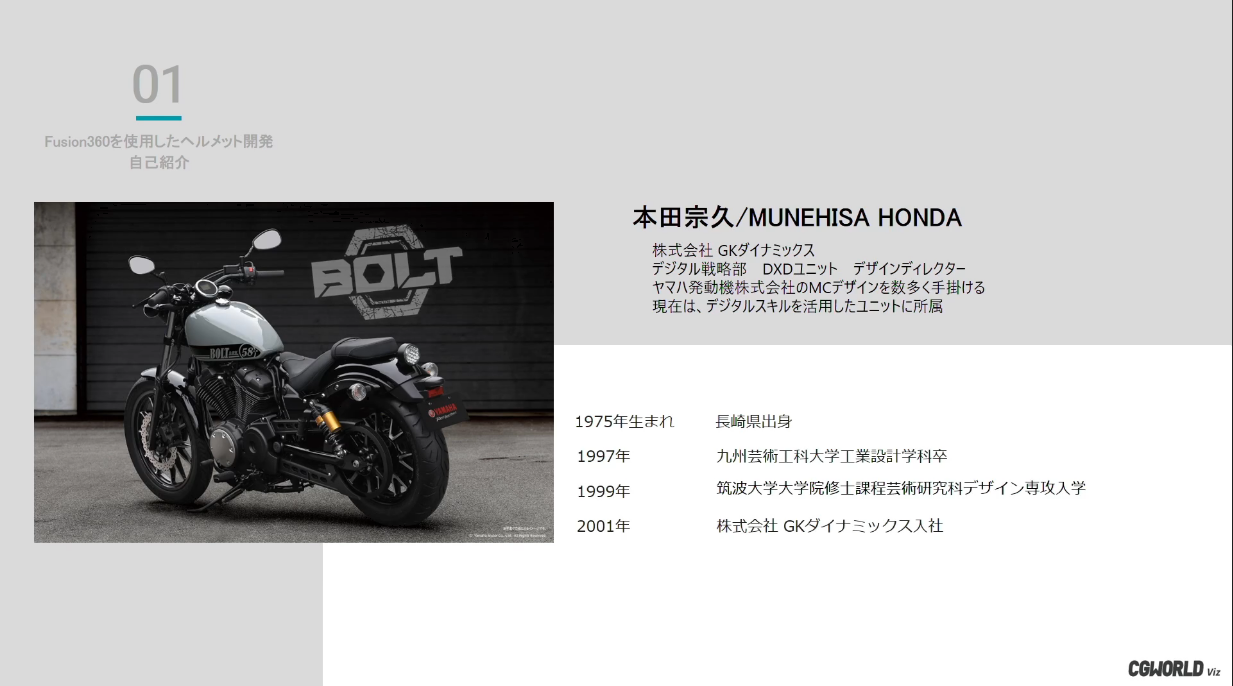
セッションのはじめは、Fusion360を使用したヘルメットの製品紹介が行われた。ヘルメットはゼット社のPROSTATUSシリーズで、同社のトップグレードシリーズに位置づけられる製品だ。
2021年度から東京ヤクルトスワローズに採用されており、テレビ中継でも日々目にすることができる。
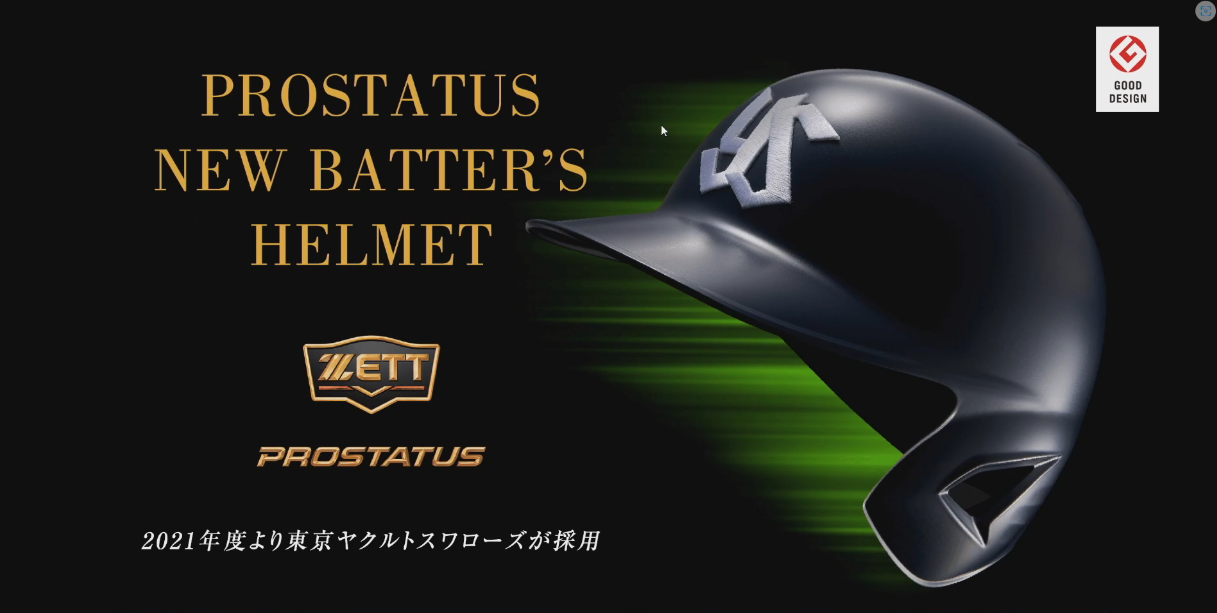
「日本のプロ野球選手が被るヘルメットでは、非常にシリアスなデザインが求められるのが特徴です。なるべくシンプルなデザインで、機能的なヘルメットが求められています」(本田氏)。
今回のヘルメット開発では、側頭部を肉厚設計にすることで、投球衝突時の砕け割れを防ぎ、安全性を向上させている。
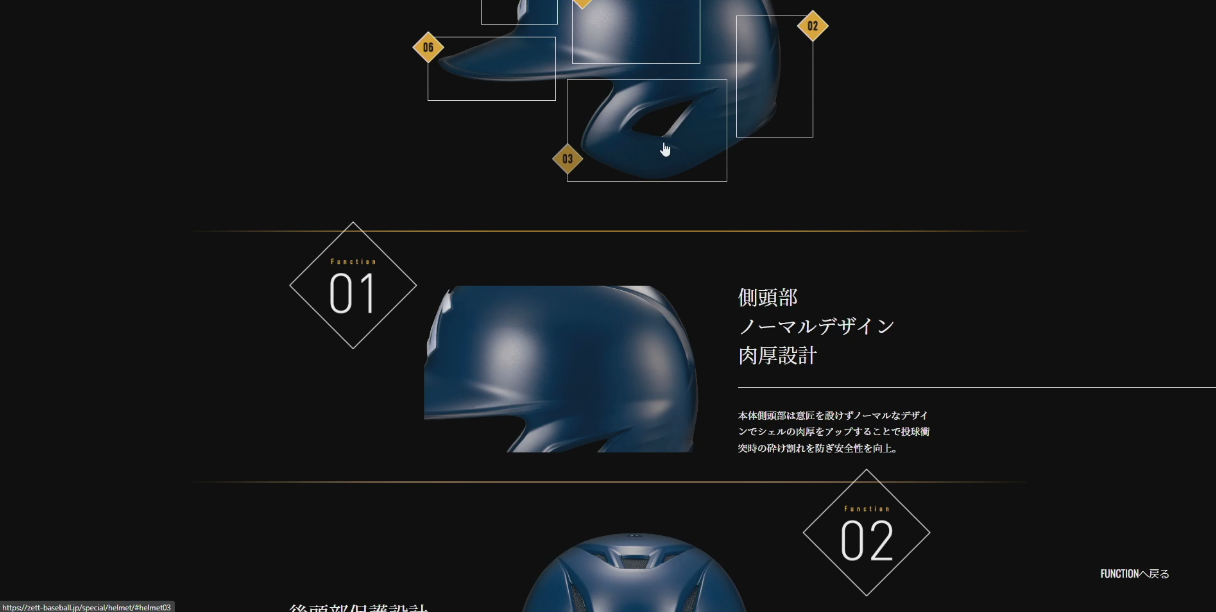
2つ目の特徴は、後頭部保護設計だ。先代モデルよりも襟足が下の方向に伸びており、これによって保護範囲を広げている。
その他にも、イヤーフラップの耳孔部周縁にリブを設けて強度を向上させるなど、安全性向上のために細部の設計にもこだわりが見られる。
「予想を裏切り期待に応える」ための4象限スケッチ
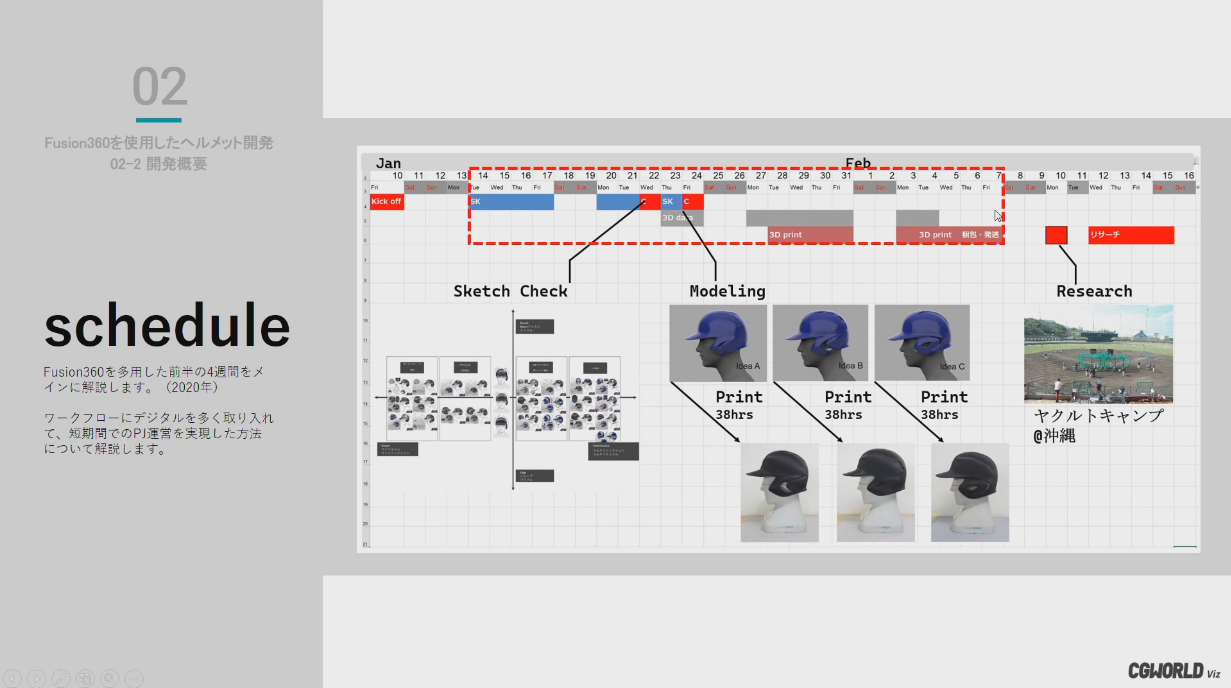
続いて、ヘルメット開発の工程がより具体的に語られた。今回は特に、Fusion360を多用した前半の4週間に焦点が当てられている。
どのような案件でも、クライアントが扱っているプロダクトの特徴を理解する必要がある。
ゼット製品の特長を分析した結果、デザインとしては、シャープ感のある流線的な形状が特徴という結論に至った。
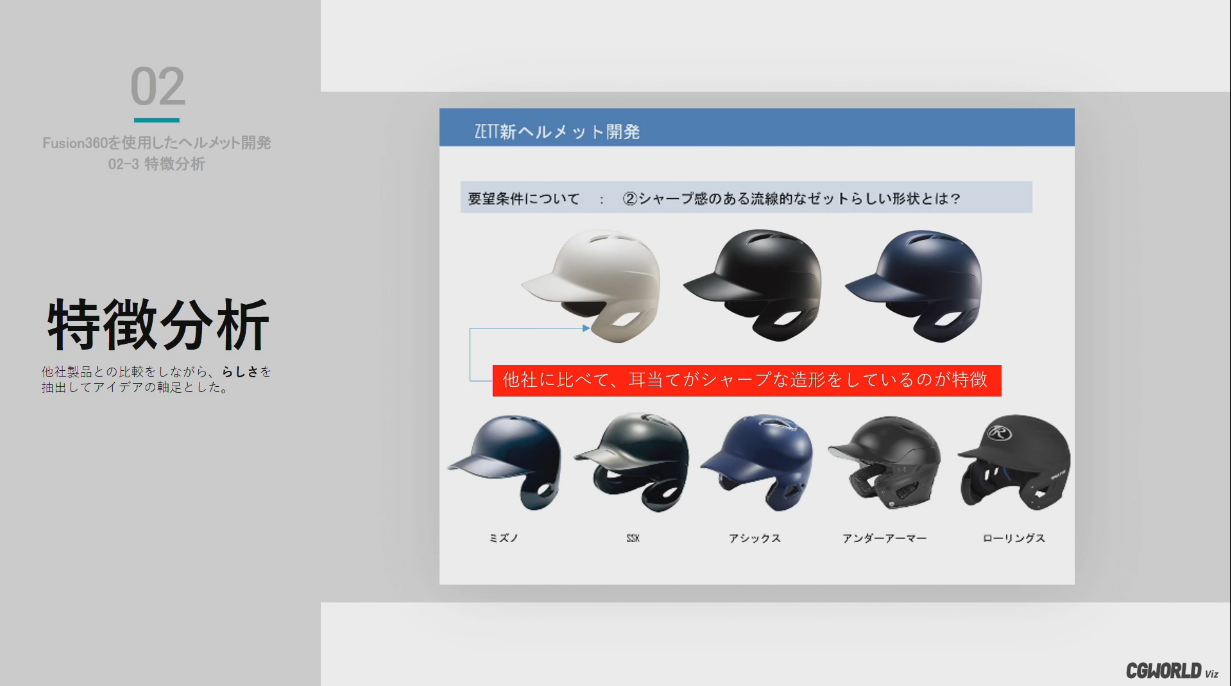
次に、アイデア出しの工程に移る。アイデアがある程度ストックされた段階で、キーワードごとにスケッチをグループ分けを行う。こうすることで、アイデアの飛躍を生みやすくし、予想を超えるアウトプットにつなげるためだ。
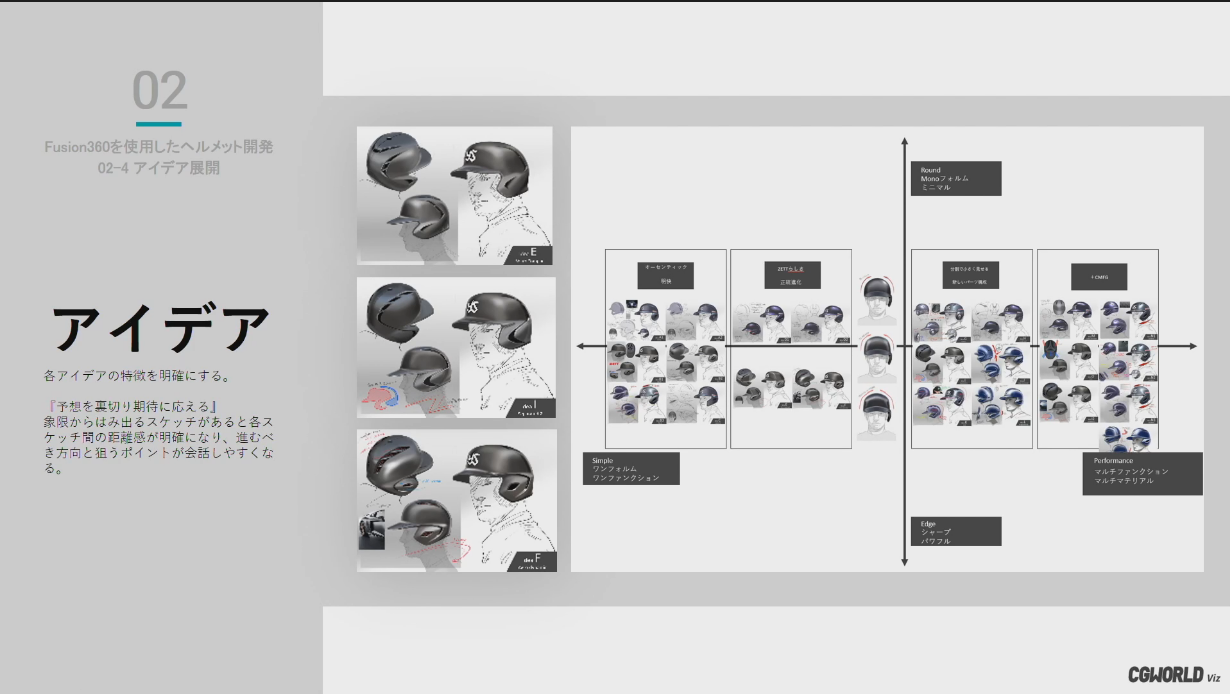
スケッチが決まった後は、いよいよモデリングとなる。タイトなスケジュールの中で納期に間に合わせるために、同社ではまだ学びたてだったサブディビジョンモデリングをベースにして、短期間で3つのモデリングを完成させることにトライした。
モデリングの際は、インナー構造を先代モデルと共用する必要があったこと、またコンパクトなシルエットはキープしたかったという意匠上の理由から、ヘルメットの頭頂部付近であるシェル構造は先代の形状を踏襲する必要があった。
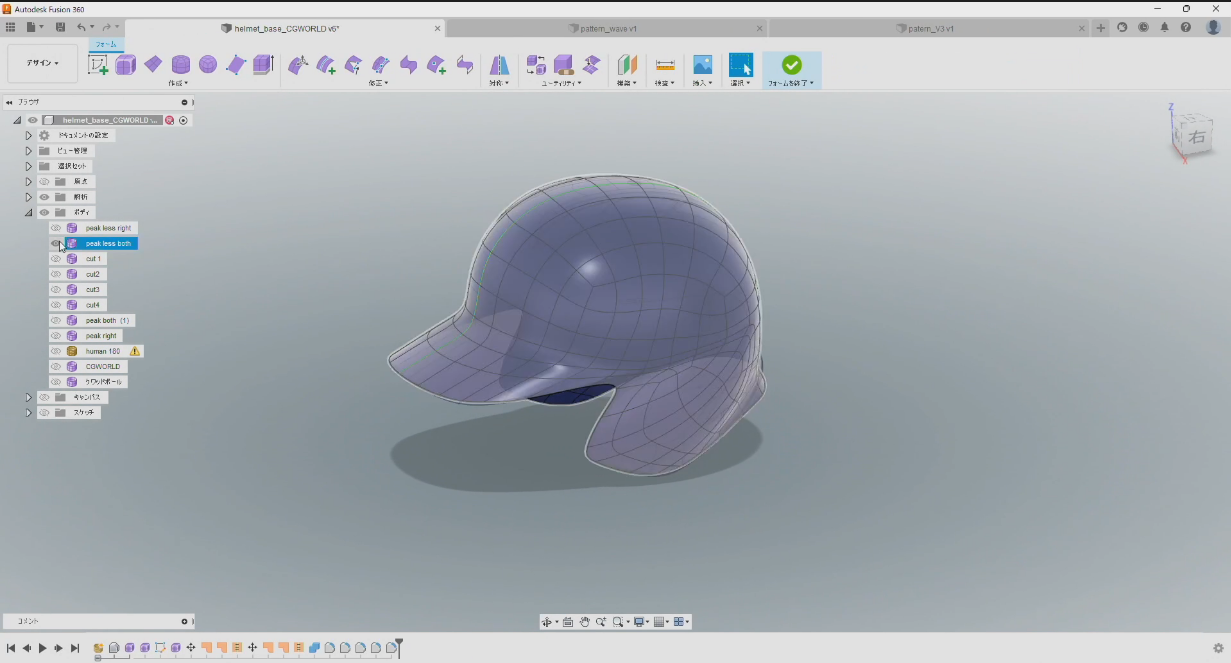
再現したいモデルが決まっている場合、どのようにサブディビジョンモデリングで素早く制作するのが適切なのだろうか。
同社では、Fusion360の「Tスプライン面を個別に作成」という機能を使った。これにより、既存のモデルに新たな面を貼っていくことができる。
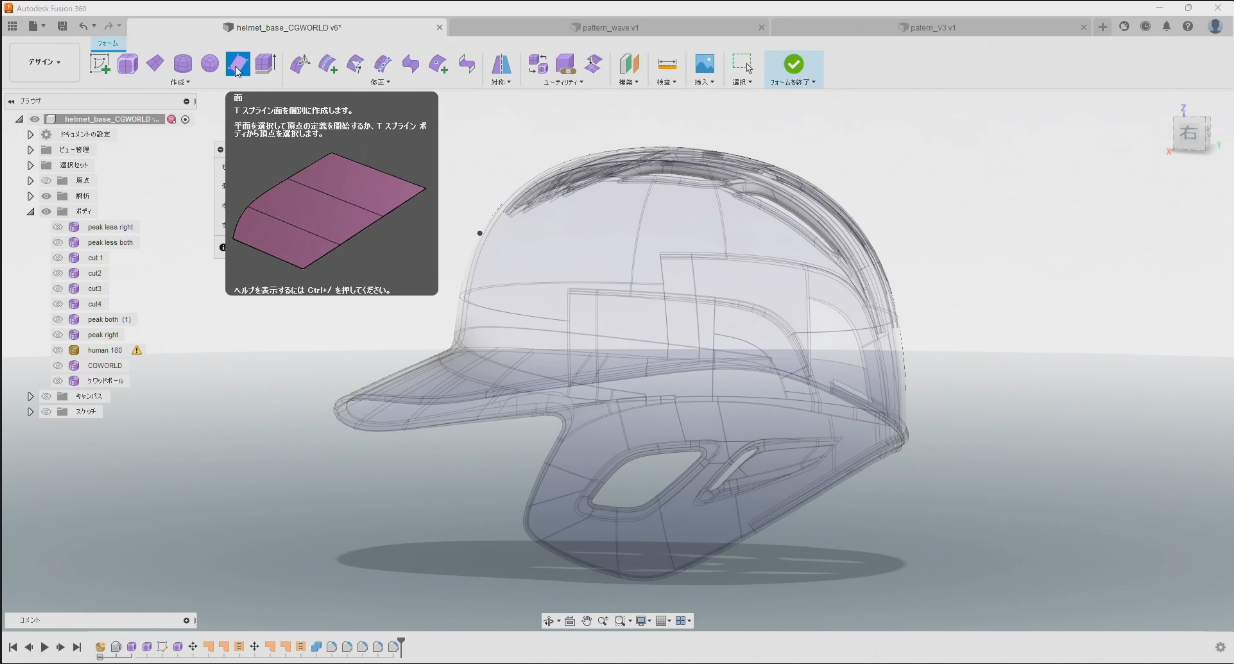
もうひとつは、「エッジ」にチェックを入れることだ。この状態でモデリングすると、連続して面を貼っていくことができるため、スピーディに作業が進む。
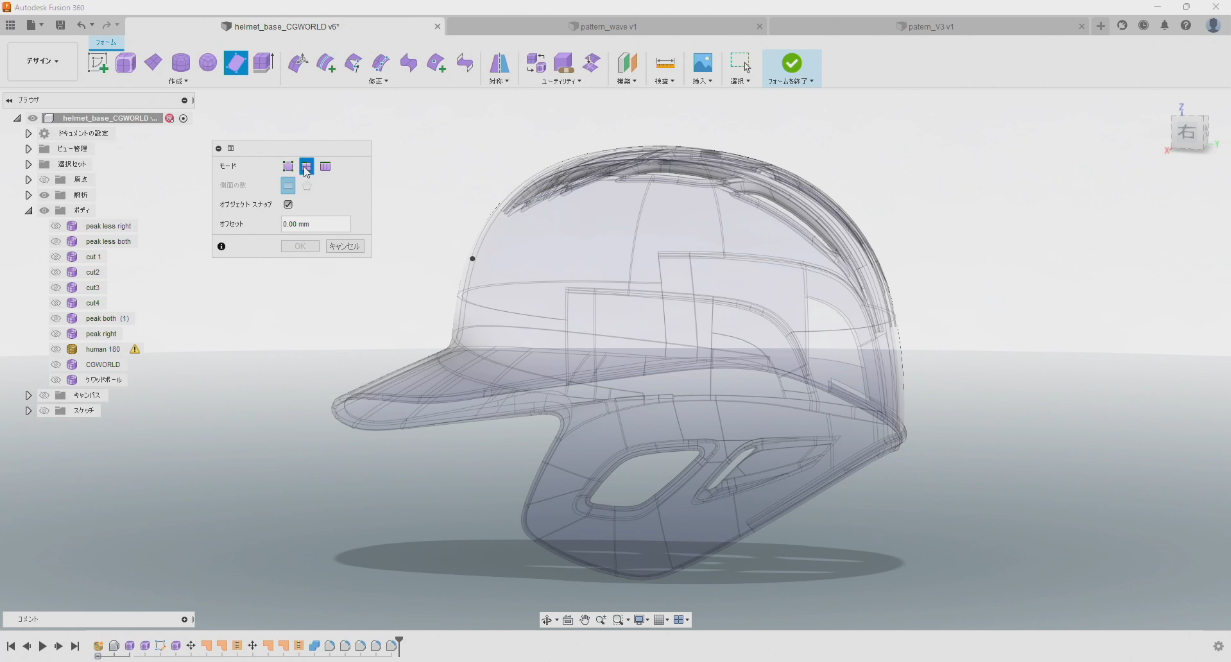
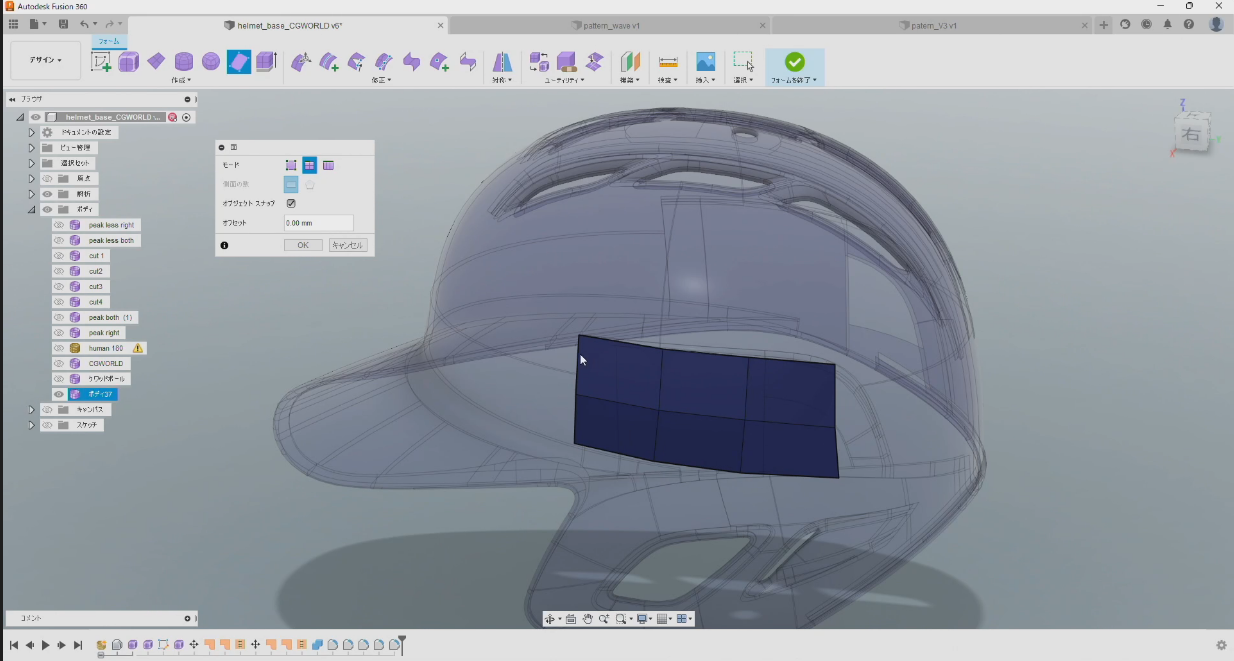
プリントアウトの工程にもひと工夫、3Dモデルのサポート部分は細かく調整
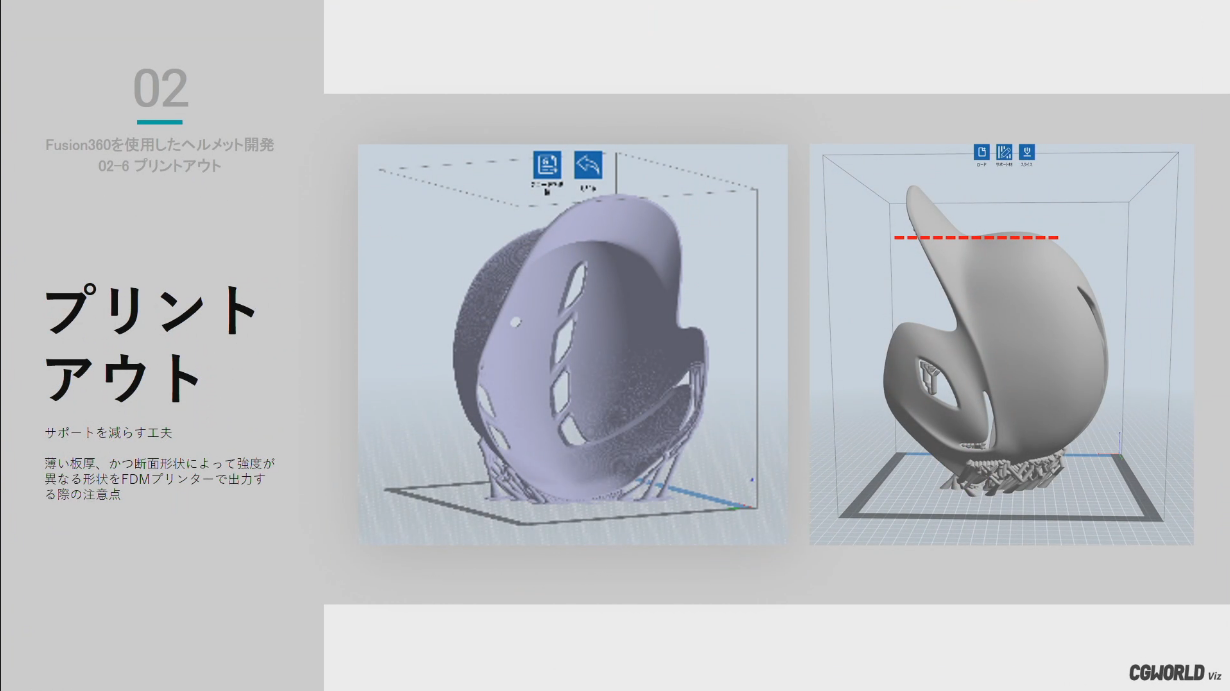
続いて、説明はプリントアウトの工程に移った。同社が使っているプリンタは300ミリ四方だが、それでもモデリングしたヘルメットをそのままの状態でプリントアウトすることはできない。
そこで、プリンタの出力のためには角度を調整し、ヘルメットを縦型にしておく必要がある。
また、3DモデルをFDM方式の3Dプリンタで出力すると、かなりの時間を要する。特に、3Dモデルをサポートする柱の部分の数が時間を要する大きな要因となる。
FlashPrintの機能を使って自動サポートを作成すると、細かなサポートが表示されるが、最近のプリンタは性能が高いため、オーバーハング部分を下から支えるサポートは全て不要となる。
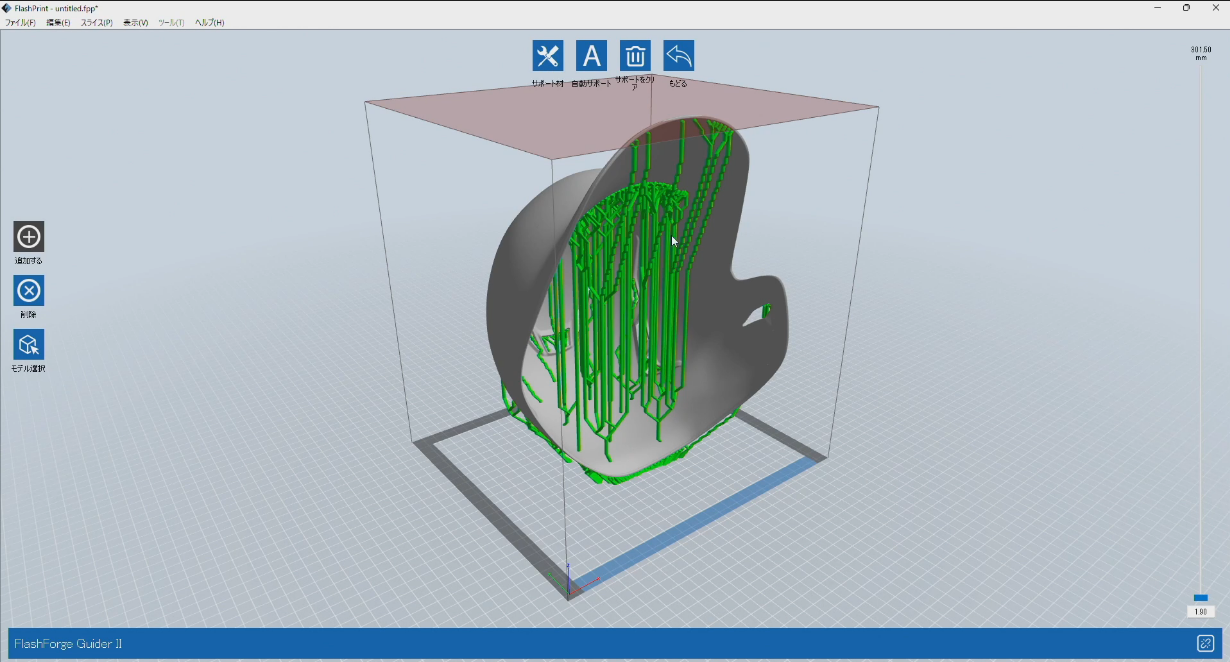
そのため、自動サポートは使用せず、手動で必要な設定を行う。今回は、直径が10ミリのかなり太めのサポートにし、プレートと接触するところのみサポートを生成するように設定する。
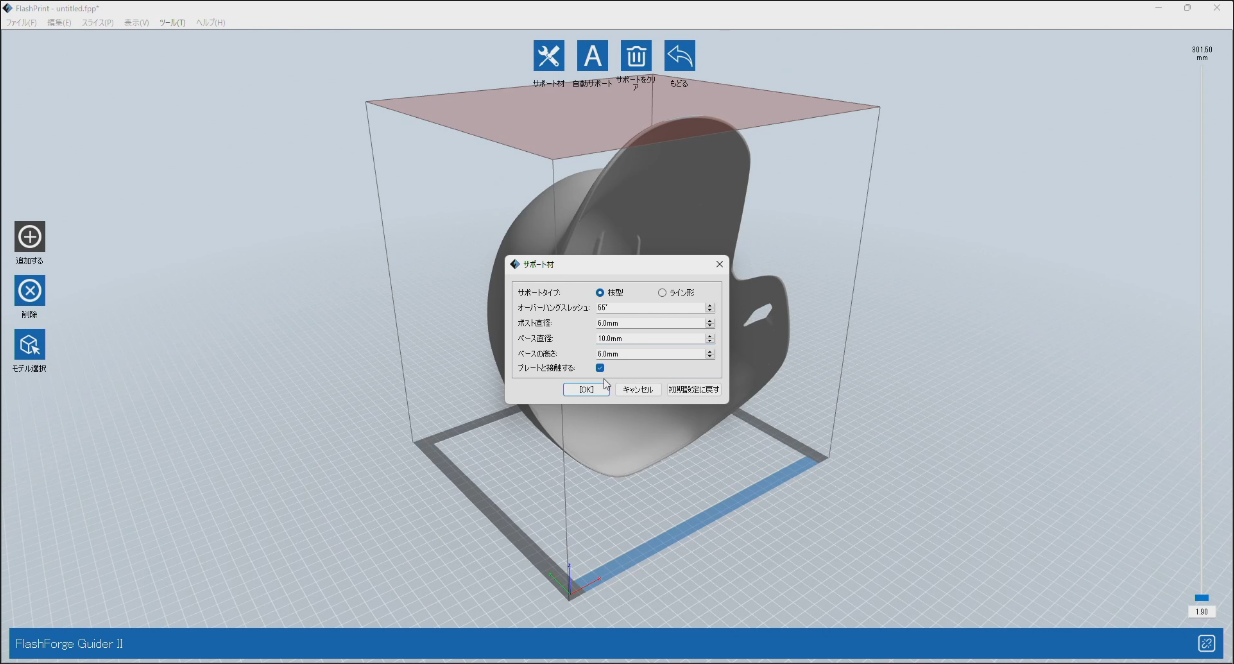
同社では、プリントアウトに関して「15h+24hの法則」を提唱している。
3Dモデルのプリントアウトに関して、長時間待つことは業務上大きなリスクを伴う。出力時間が長くなればなるほど、失敗の可能性が高くなるためである。業務時間中にプリンタに気を取られると作業効率も落ちるし、納期が近いと大変なストレスになってしまう。そこで、なるべく夜間に稼働させ、日中はプリンタのことを気にしないようにしたい。以下の図のように、1日目の定時にセットしておけば、退勤後の時間を最大限活用することができる。
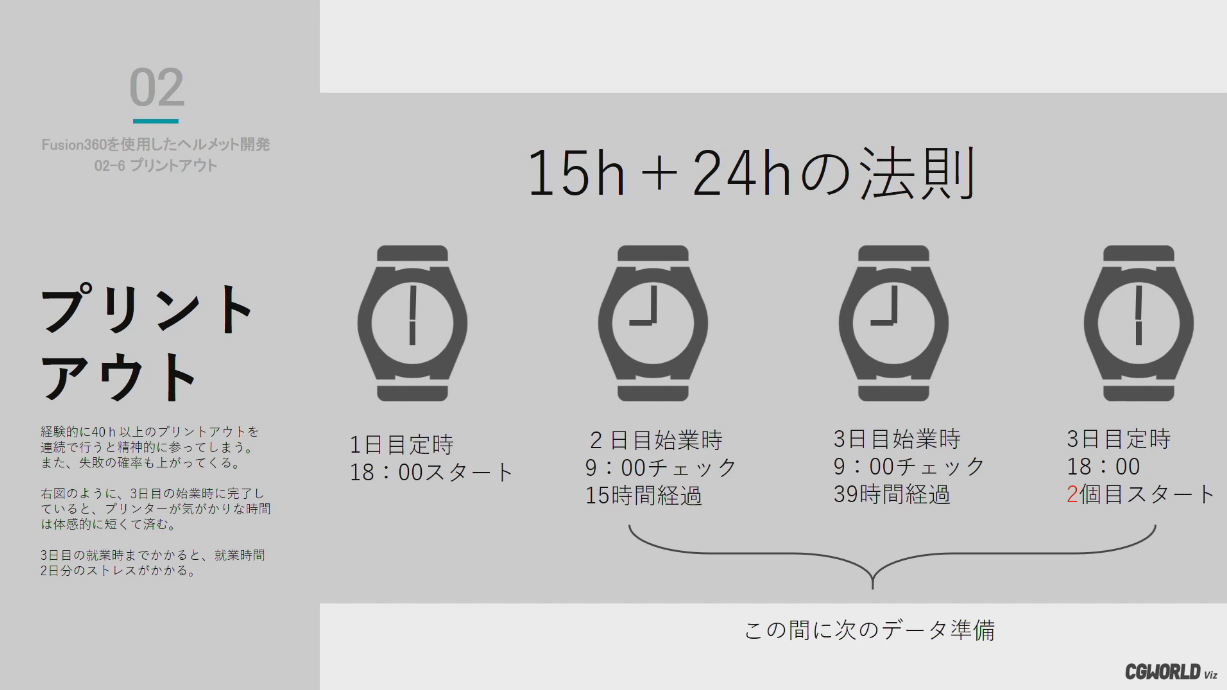
3つのプリントアウトが完了すると、選手へのリサーチを行う。完成したヘルメットのプロトタイプを鏡を前にした選手たちに被ってもらい、使用感やビジュアルに関してコメントをもらった。
客観的な強度解析でデザイン改善と強度の向上を実現
ここまでが4週間の主な動きになるが、その後、もう少し製品の特長を出していきたいという意見があったため、パラメトリックデザインを織り込んだ強度と外観的特徴の向上を図るプロセスへと進んだ。
「市場にはパラメトリックデザインが含まれる製品が多く存在していたため、その中のいくつかを参考にアイデア出しを行いました」(本田氏)。
そこで、見た目はシンプルかつ特徴が際立つようにデザインを再考することになった。
強度解析に関しては、Fusion360の「静適応力」機能を使用した。ヘルメットの一部分を切り取り、目指すパターンに近い断面を表現。片側を固定し、もう片方に力を入力することで、どのような形状が強度に寄与するのか検討した。
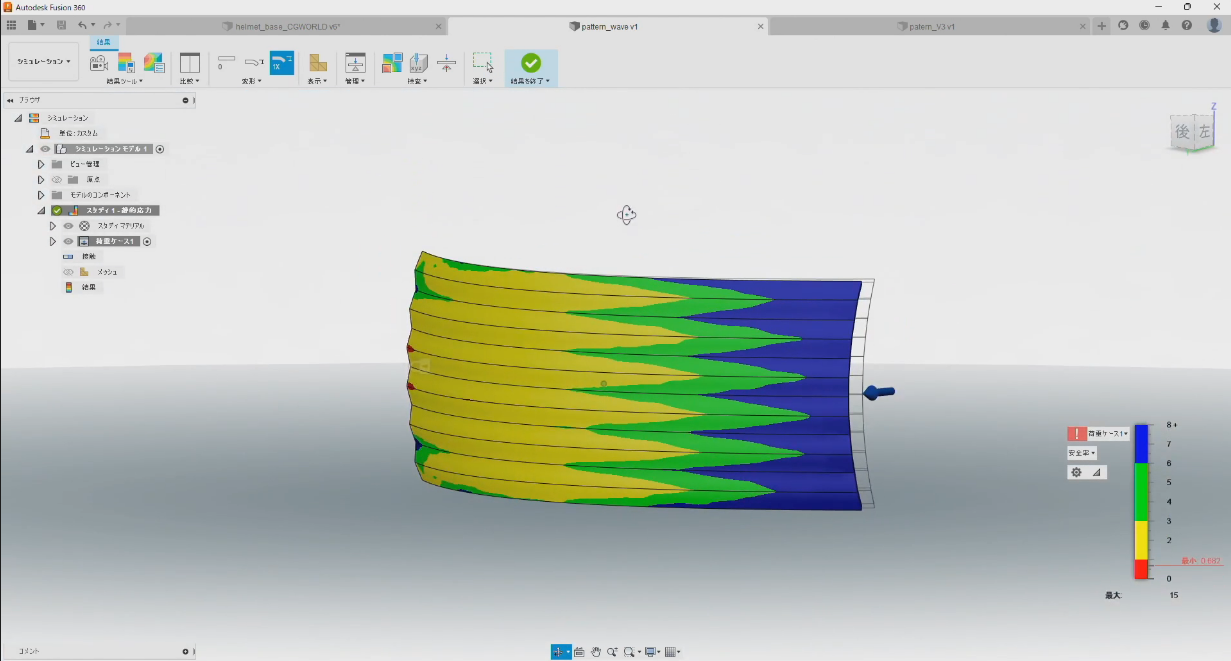
「Fusionの機能を利用して、感覚だけでなく数値を確認しながら客観的に強度の向上をさせることができた点が良かったですね」(本田氏)。
Fusion360には「動的イベントシミュレーション」という機能が備わっているが、静適応力機能の方が設定が簡単であり、エンジニアからもシミュレーション結果に間違いはないという声があったため、今回は静適応力機能のみを使用している。
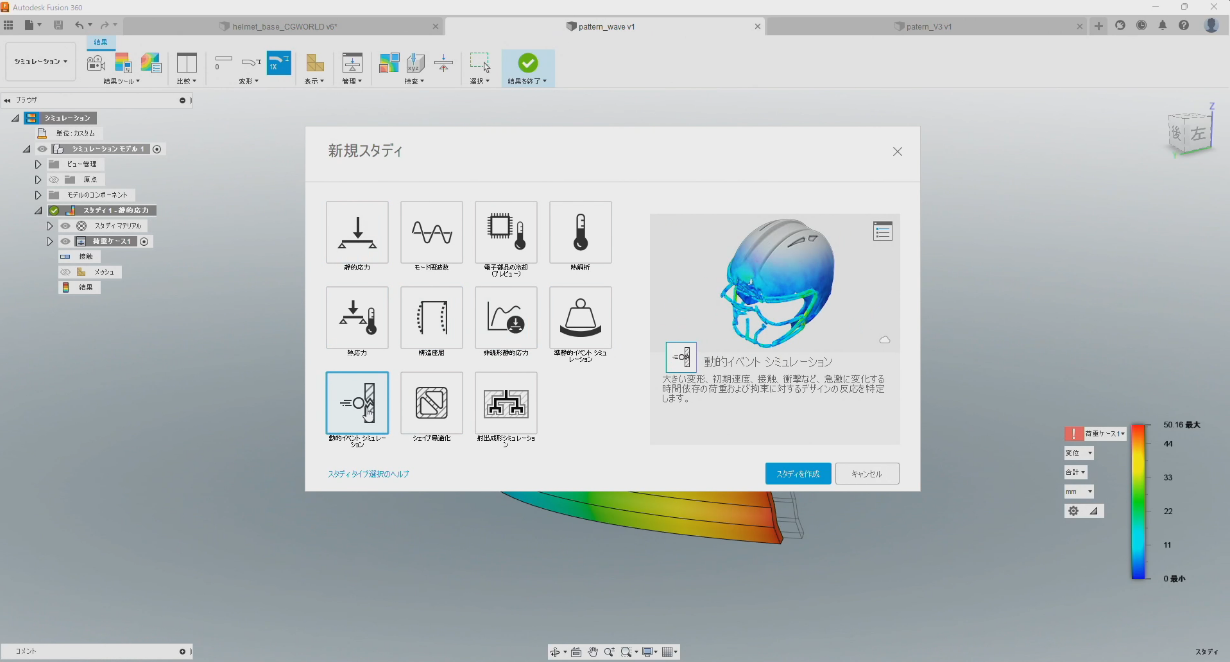
最終的には、新作は既製品に比べて頭が小さく見える形状にし、側頭部はシャープな造形、頭頂部は新規性のある形状、襟足部分は強度の高い形状に変更された。
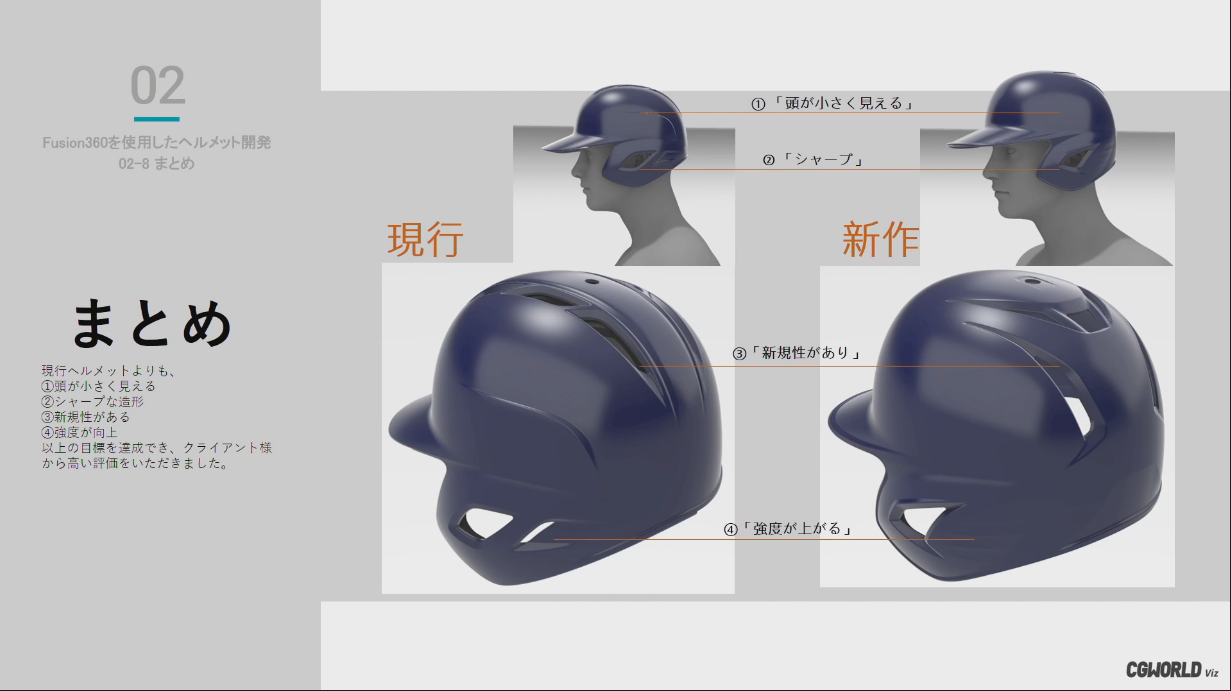
最後に、GKダイナミックスの主な活動が紹介され、セッションは終了した。
TEXT_江連良介 / Ryosuke Edure
EDIT_小村仁美 / Hitomi Komura(CGWORLD)